Akadobe kiln-changed 5-go sake cup by Seiichi Onishi
Akadobe kiln-changed 5-go sake cup by Seiichi Onishi
Couldn't load pickup availability
Height: 21.5cm Width: 7.5cm x 8.0cm
Box Height: 24.5cm Width: 12.5cm x 12.5cm
About Tanba-yaki red clay kiln change
The history of Tamba is long and is said to have originated in the Kamakura period.
The anagama era ended in the Edo period, and then changed into the climbing kiln era, which continues to this day.
Akadobe ware is fired in these climbing kilns and is always featured in old books introducing Ko-Tamba ware, representing works from Ko-Tamba (before the Meiji period).
If it were possible to recreate the beautifully fired red clay pottery of the past in Tamba today, it would undoubtedly become an Important Intangible Cultural Property of Japan, something that has never been achieved since the beginning of Tamba ware. It would be so valuable that it would undoubtedly become such a property.
Seiichi Onishi is also working hard every day to get even a little closer to this standard. Among the many Tanba ware kilns, he is the only one that fires all of his pieces in a climbing kiln (made from split pine wood) for about three days and nights.
The works fired in the climbing kiln include Akadobe and Shirotanba.
The Akadobe variety is characterized by its reddish base color, with a strong, astringent flavor.
Shiratanba ware has become popular in recent years as it has a natural color that can be achieved simply by applying white mud.
If you use this piece for a long time, it will eventually develop a "used" character (a darkening) and change to a very nice color.
Yakishime kiln-hen seeks out the ancient kilns that are the origin of Tamba ware, and only uses climbing kilns unique to Tamba, whose shapes and firing methods have been passed down since the early Edo period.
In this climbing kiln, split red pine logs are used as fuel for firing.
No glazes are used, and the piece is not bisque fired. Instead, the piece is fired by placing split pine logs directly against the piece. The force of the burning pine logs brings about various changes in the piece, which is called kiln change.
Red clay kiln-transformed 5-go sake cup
- Akadobe : This refers to the type of clay used in the piece. Red clay has been used since ancient times in Japanese pottery, and has a unique texture and color. Tanba clay is rich in iron, and when fired, the iron in the clay turns red due to the formation of iron oxide.
- Yohen : Yohen refers to the natural change in color and pattern that occurs during the firing process in a kiln. This gives each piece of pottery a unique character.
- Gogoiri : Gogo is a unit of volume and refers to approximately 900ml (just under 1 liter). A Gogoiri choshi is a size that is especially used when enjoying sake.
- Ochoshi : A choshi is a vessel for pouring sake. It is traditionally used during banquets and ceremonies.
This choshi is characterized by the warm color of the red clay and the natural patterns created by the kiln transformation. It is a work that reflects Seiichi Onishi's outstanding technique and unique aesthetic sense, and you can appreciate its value not only by using it but also by appreciating it.
Share
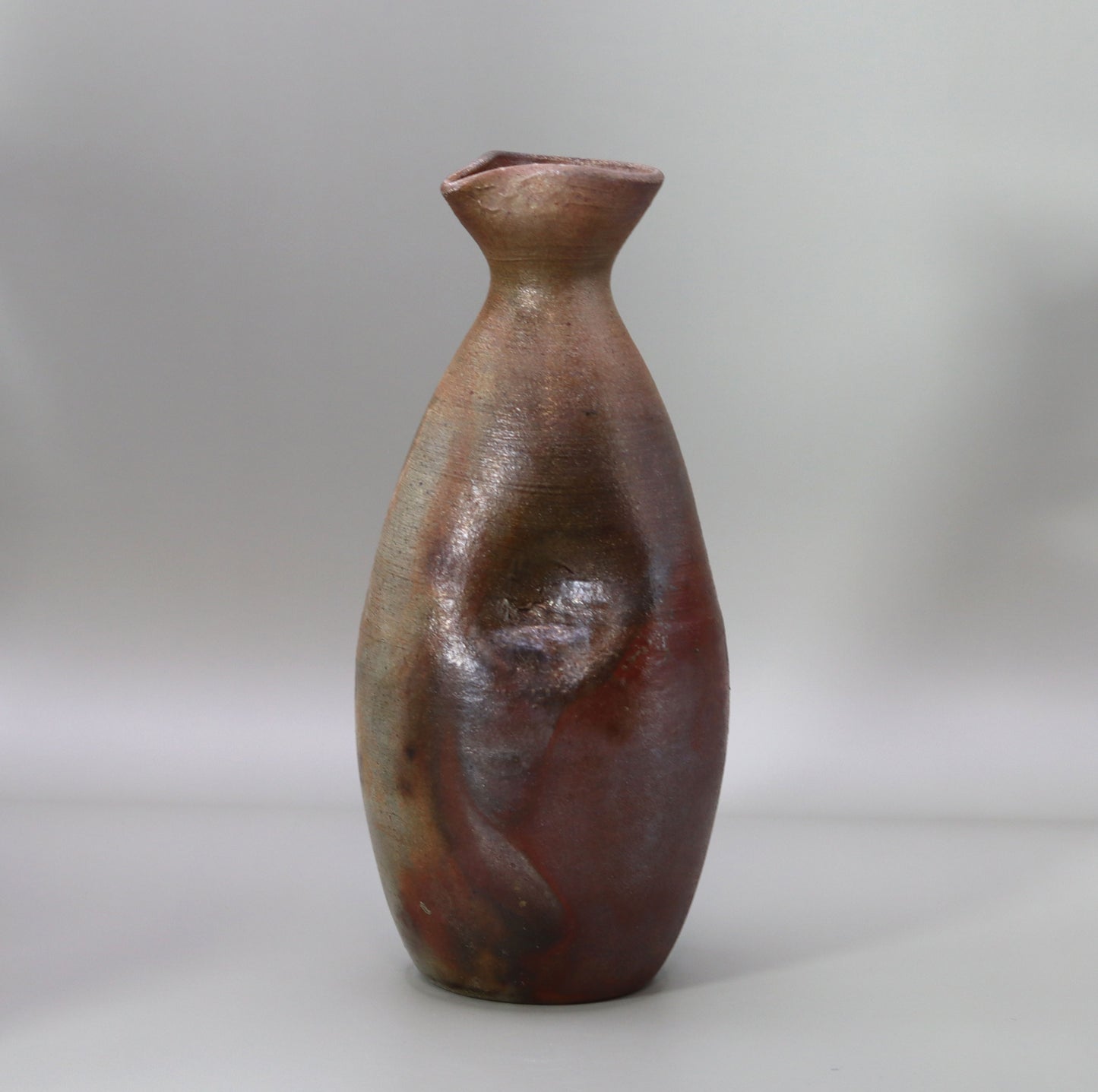
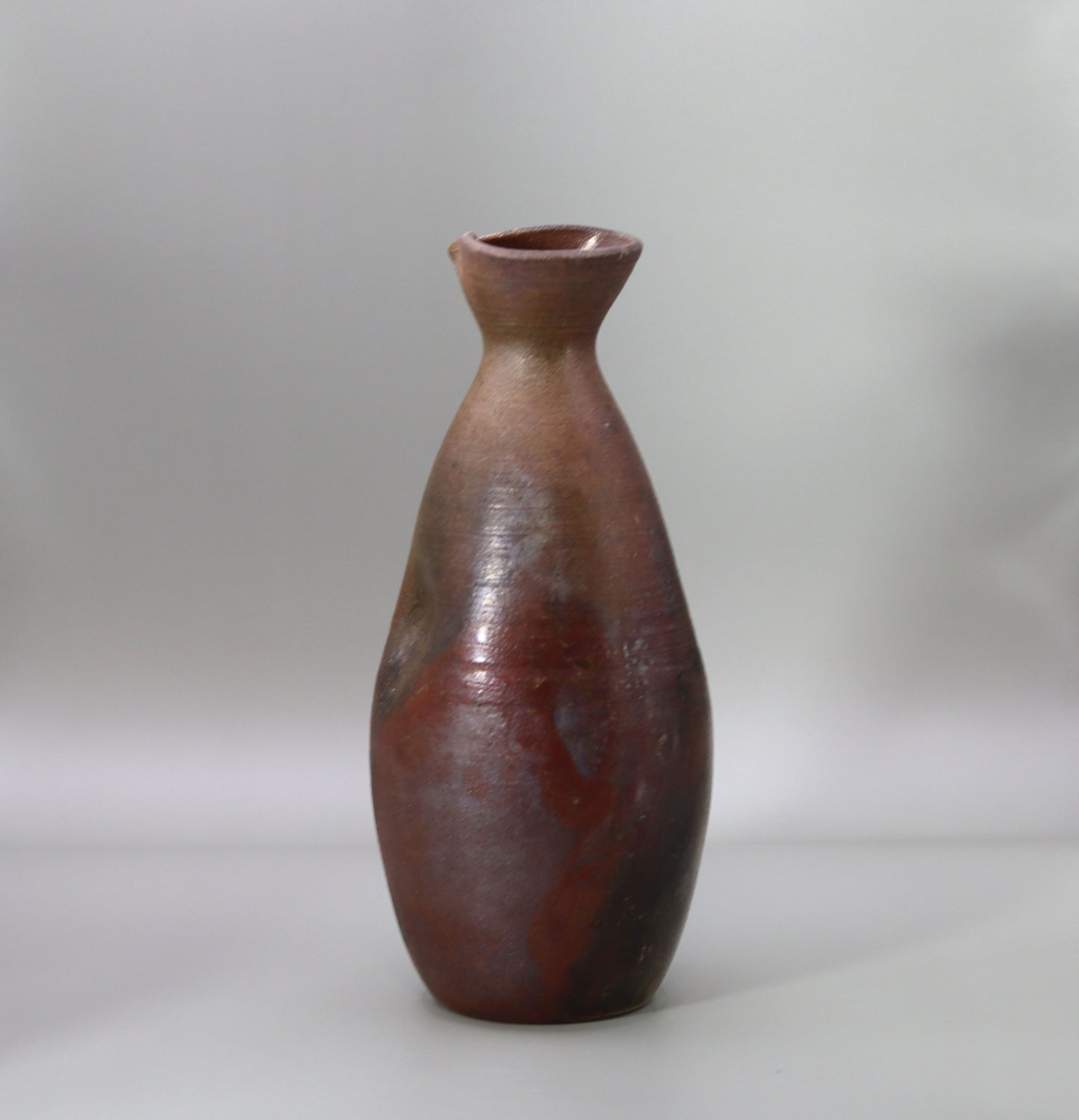
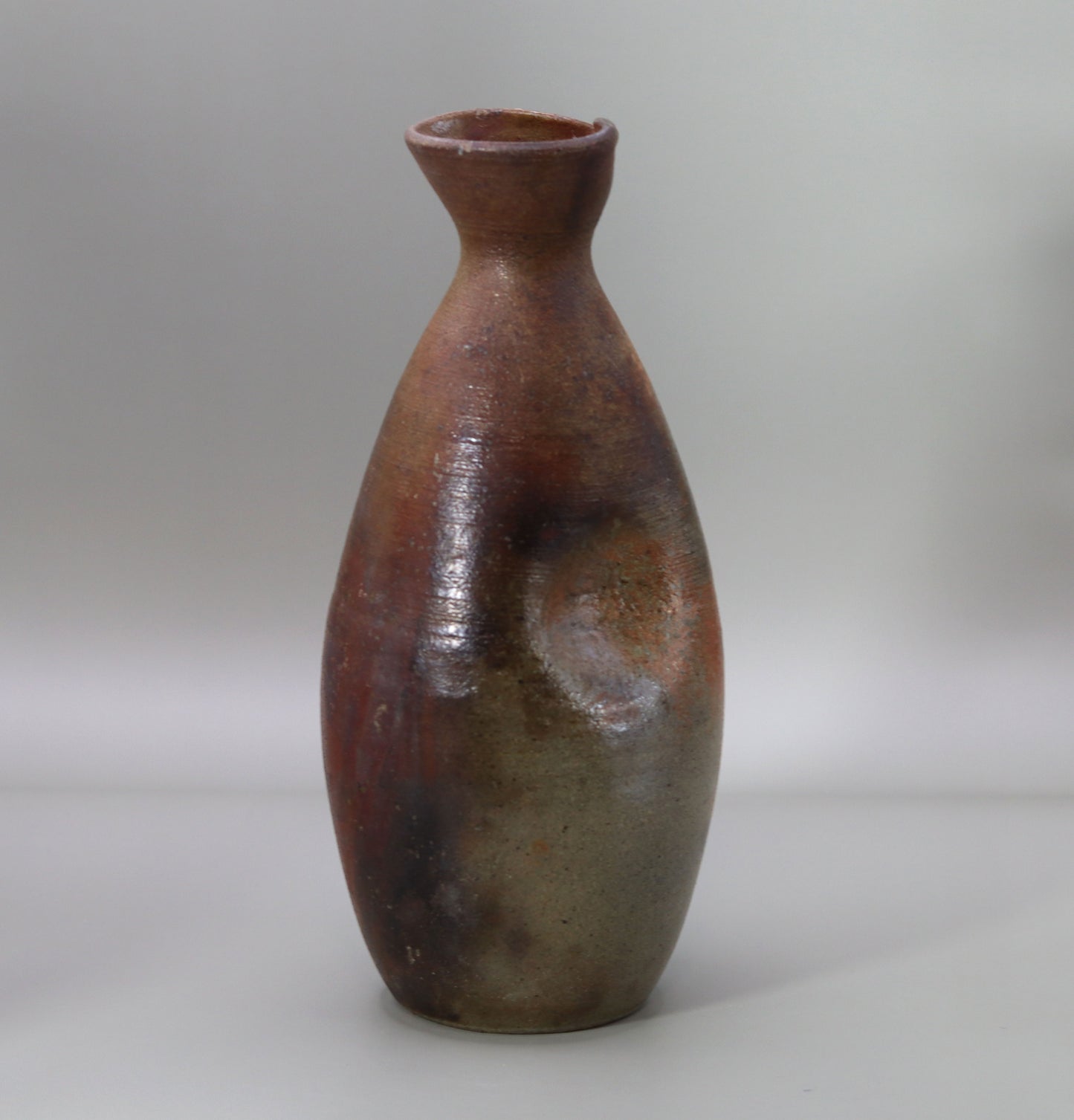
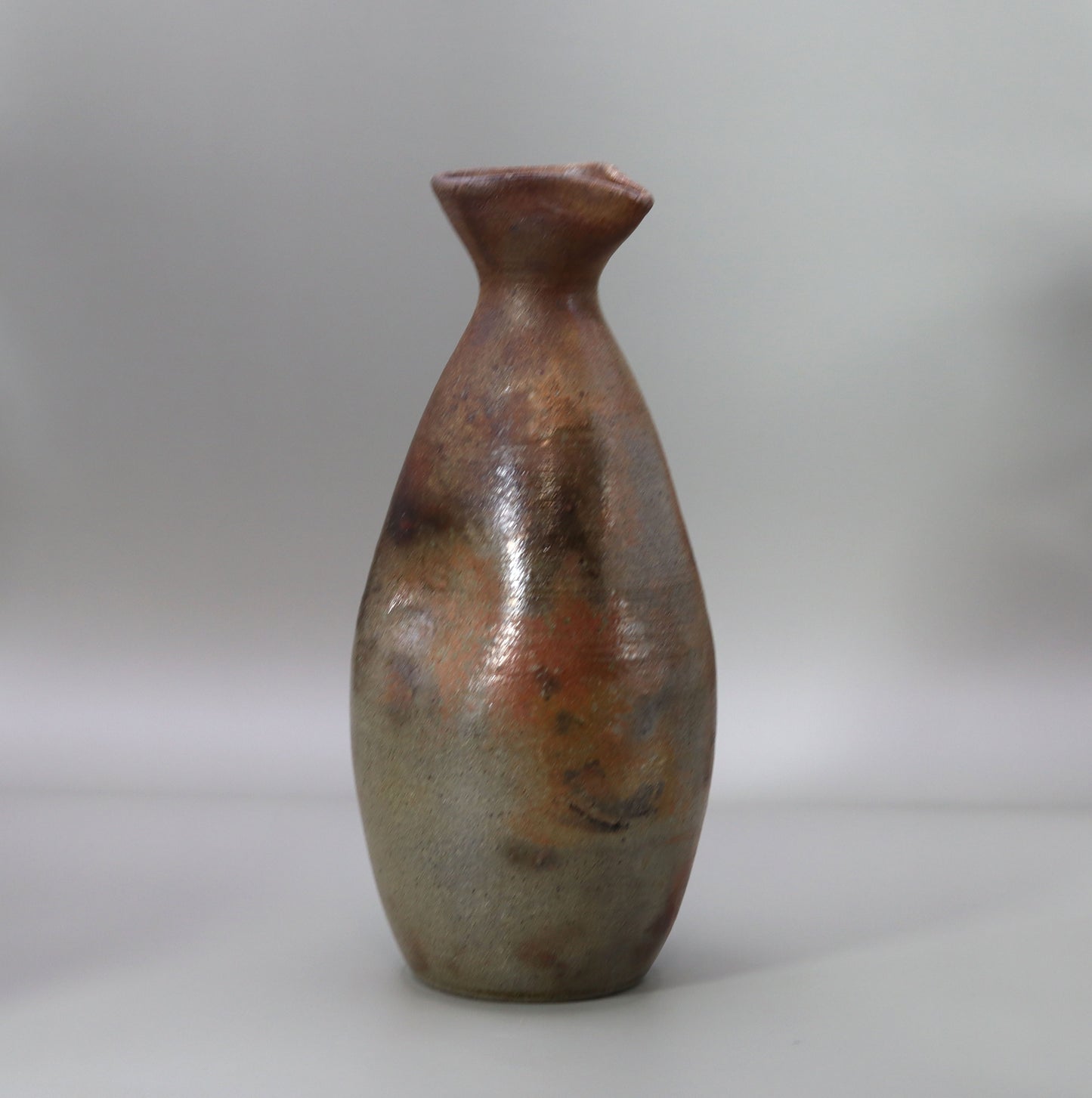
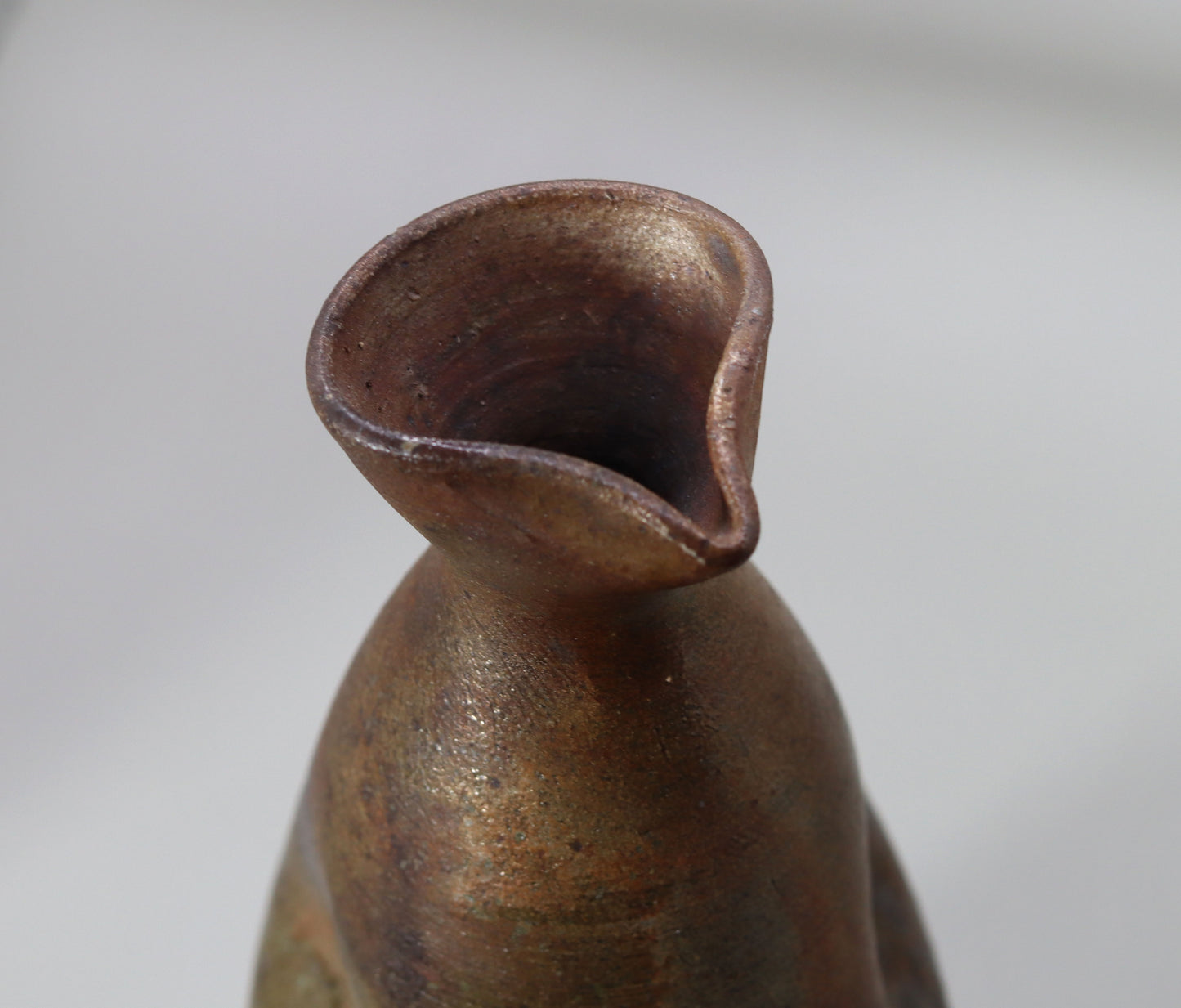
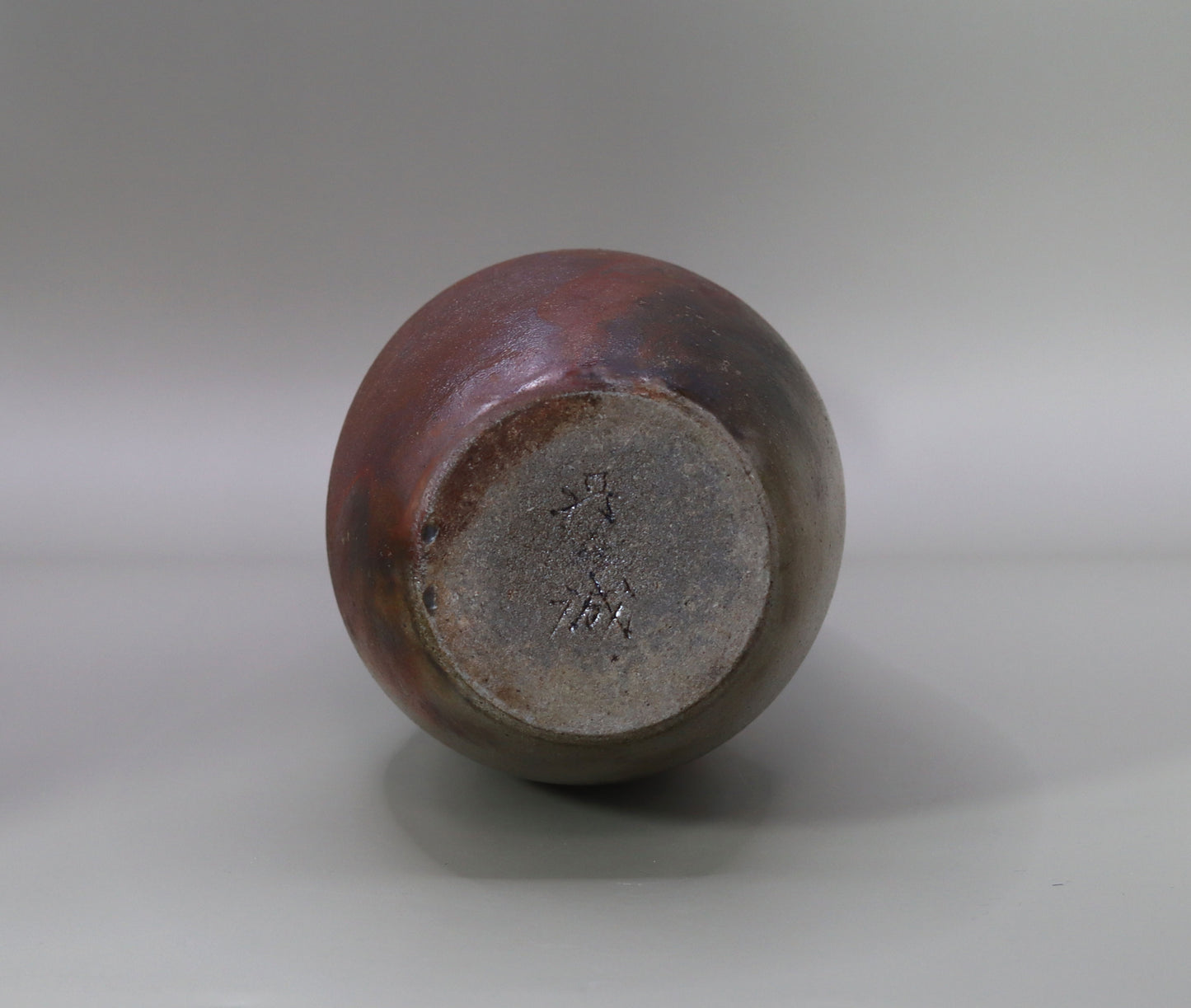

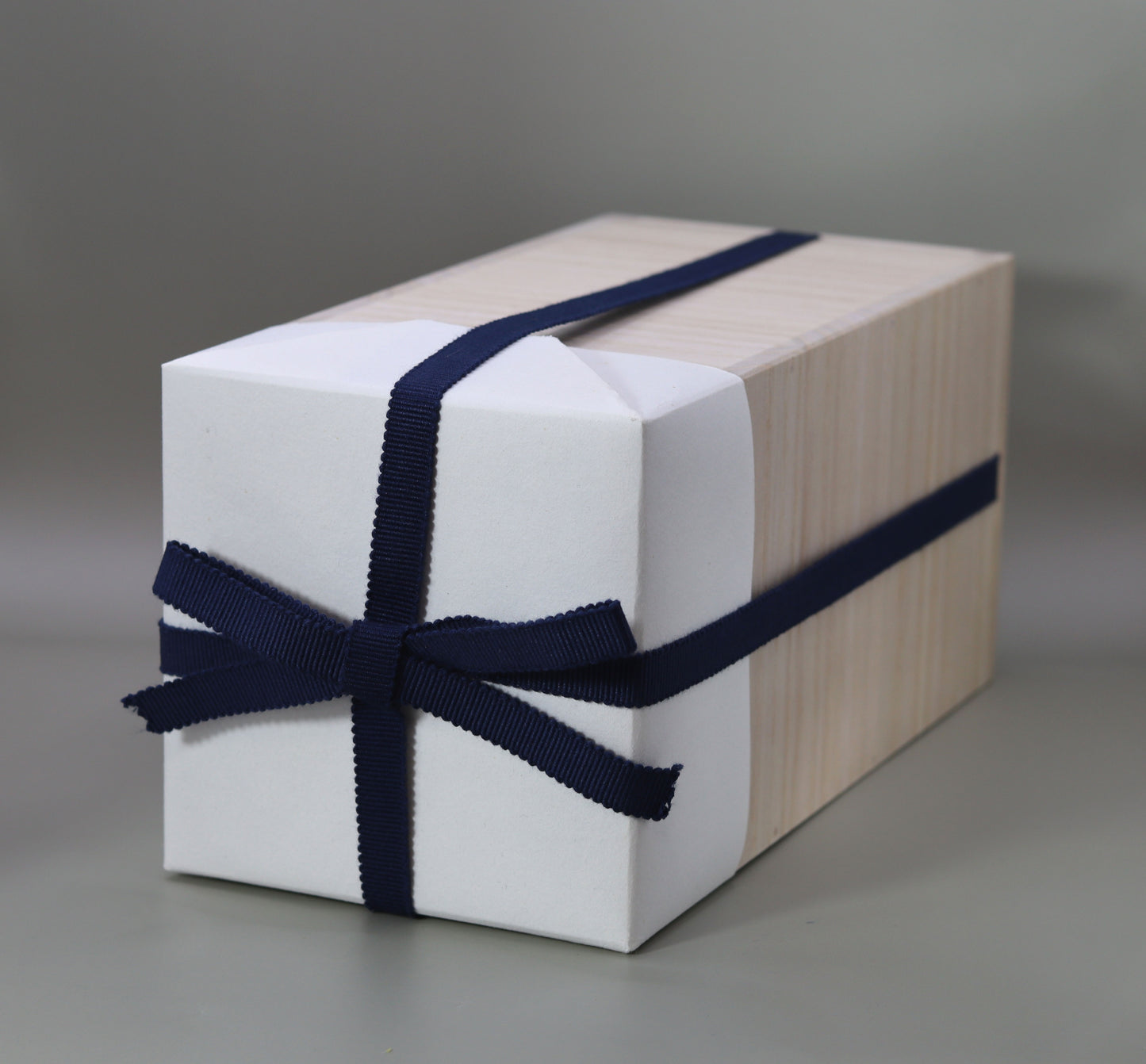
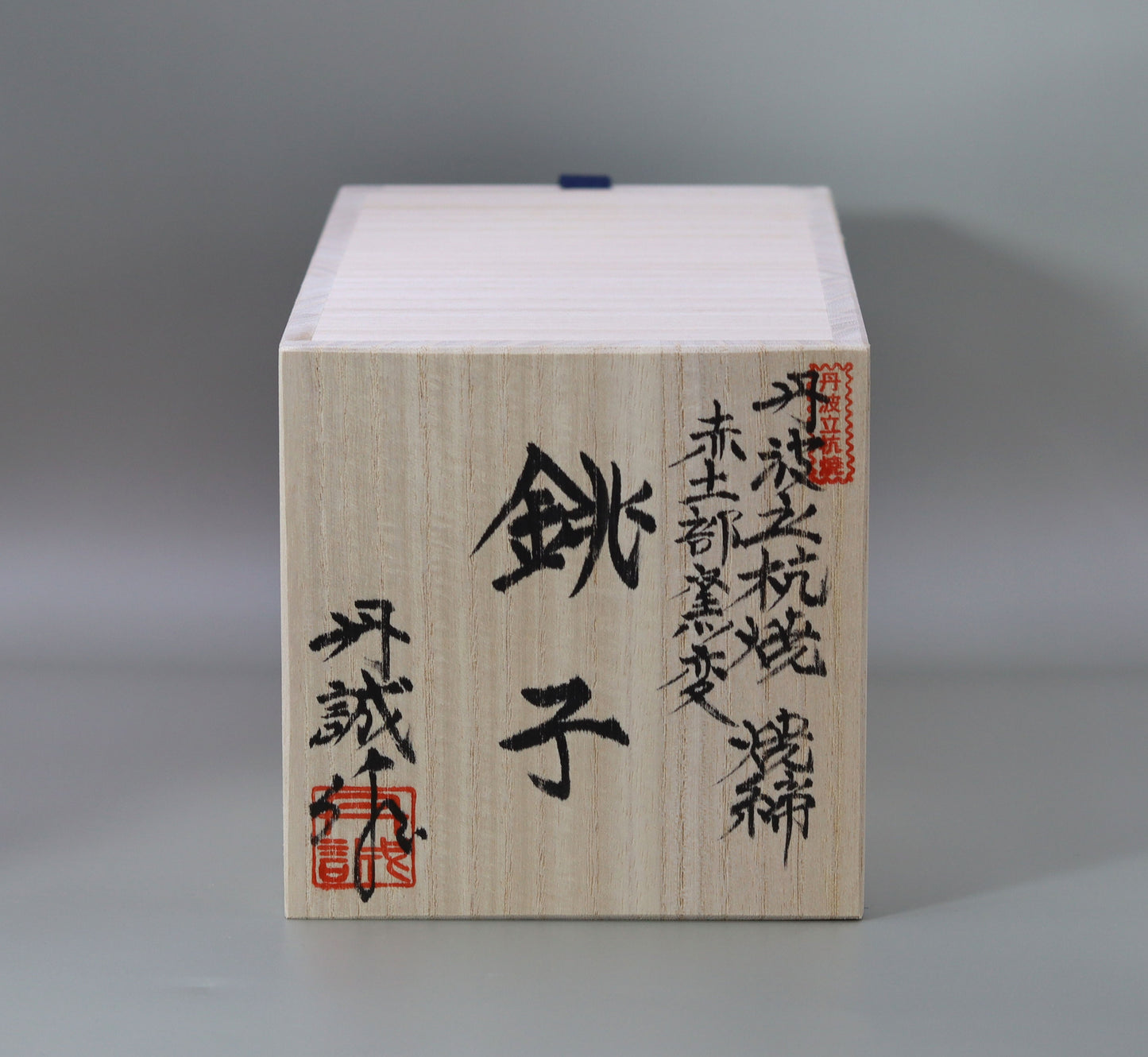
Multi-Column
-
[I will send it to you quickly and carefully]
We carefully package each product in a way that suits it best.
Also, delivery times vary depending on the piece (vessel, etc.).
Items that already come with a box will be shipped within 1-3 days of the order date.
For items that require a box to be made after your order, it will take approximately 30 days for production to be completed and then shipped.
In either case, once we have confirmed your order, we will contact you by email to inform you of the delivery date.
-
[Requests when purchasing pottery]
Even products that look the same may differ slightly in color, shape, size, etc.
The way the glaze is used, the power of the kiln, the firing method, the season, and the humidity also affect the appearance of the pottery.
Please understand the individuality of each piece of pottery and enjoy the unique warmth of handmade.